Testimonials
![]() | Larned. Kansas |
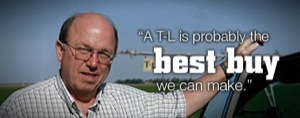
![]() | Plains, Kansas |
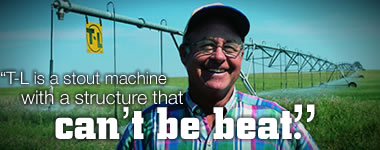
![]() | Garden City, Kansas |
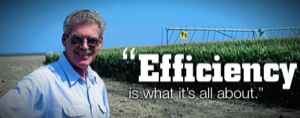
![]() | Clay Center, Kansas |
As Steve Peterson, Clay Center, Kansas, learned, there’s more to T-L Irrigation Company than being a manufacturer and marketer of pivot systems. Farming 1,500 acres and pumping water from a river, he had seven non-T-L sprinklers–and a continuing problem. His setup simply couldn’t provide the necessary capacity that would allow him to apply water over his cropland fast enough. Besides being behind all the time, he also kept having pump bearing problems at the worst possible times. Then he started talking to a neighbor, Bob Wietharn, who in addition to farming 1,200 acres of corn and soybeans was also a T-L dealer. While the easiest redo solution would have been to start completely from scratch, that option wasn’t feasible due to prohibitive costs. So, Wietharn worked with T-L’s Pump/Power Division, blending his knowledge of the area and Peterson’s specific needs with T-L’s expertise. Although usually helping design new irrigation setups, the Pump/Power Division can also be called on to suggest improvements for existing sprinkler irrigation installations. The primary teamwork objective in this instance was to come up with a solution that would get the water on when needed and utilize some less expensive alternatives. Peterson quickly implemented the primary recommendation of replacing his two existing pumps with a pair of Cornell pumps. And, what a payoff! As Wietharn explains, “This change alone increased his efficiency enough that each of his twin John Deere six cylinder engines and Cornell pumps were able to, almost double the amount of water available (from 750 gpm to 1400 gpm) at 100# discharge pressure at the pump. “The reason for that much pressure was that some of the water has to be pumped two miles through a pipe not really designed to handle so much water.” he adds. “Now his pumping setup is efficient enough to run four pivots instead of two, as before.” Oh yes, thanks to the additional capacity available, Peterson was able to install an eighth sprinkler system, another T-L. Although it’s still making its first circles, one feature has already caught his attention. As he notes, “Once I turn on the water I like not having to go out and punch buttons to turn on the pivot, too. The pressure switch automatically does this for me.” “Customers may at first think that a T-L installation costs more,” Wietharn observes. “But, we’re always looking long-term and designing a system to get the quickest payback. “You know,” he continues, “you can buy something cheap and then pay for it in the long run. Or, you can buy something maybe a little more expensive that’s also more efficient that returns your money sooner. That’s why a farmer should look at a T-L system as an investment rather than an expense.” Incidentally, Wietharn also ran non T-L electric sprinklers for a number of years. What caused him to change to T-L was the continual headache of being forced to replace electric motors and gear boxes. Then, too, his brother-in-law’s two T-L systems had recorded only one stop in a combined 35 years of operation. That was the clincher in his decision. Wietharn’s system benefits irrigators who must pump from low water rivers or tailwater return pits. He’s the inventor and manufacturer of the Riverscreen(TM), which is available through T-L dealers. Irrigating from a river that usually can be waded across, his sprinkler nozzles kept plugging up with debris that was sucked through the system. Cottonwood fuzz was the worst offender. A screen over the pump inlet that prevented sticks from entering would then plug up with the cottony fuzz. Conversely, a screen large enough to let the fuzz through also allowed larger debris to enter. “At certain times I’d have to spend several hours a day cleaning nozzles, not to mention cleaning filters.” Wietharn recalls. “I finally decided I’d either have to come up with something different or quit watering through a sprinkler.” His answer was the Riverscreen(TM), which can allow pumping from a depth as shallow as a four inches in running water. An optional power drive requiring as little as six gallons per minute can be added for use in slow moving water, tailwater return pits, and manure lagoons. Another option is a galvanized lifting boom with a brake winch. This boom lets one man quickly swing out and gently lower the Riverscreen(TM) to the water’s surface where it floats in place on four pontoons. The screened, rotating drum measures 32×48 inches, and rests on an aluminum frame. Four inches of water isn’t much, yet that’s enough depth, according to Wietharn. That’s because he designed his unit to draw from an area approximately seven times the size of the suction line that typically operates on a velocity of less than five feet per second. As a result, the Riverscreen(TM) can operate anywhere there is four inches of water above a stream’s bottom. Water moves past a series of paddles which force the drum to rotate and clean itself of debris. Six, eight, and ten inch models are available, also a four inch unit with an 18×24 inch drum is available on special request for low gallonage pumping into high pressure end guns. “The three Riverscreens(TM) I use have eliminated any trouble I was having pumping out of shallow water,” Peterson sums up. “I used to have to walk my sprinklers every day to unplug nozzles. Now I rarely ever have to unplug a nozzle, and I can utilize a cost effective pivot sprinkler system on my crops.” T-L DIVISION Provides Design Know-How Plus Components “Our goal,” emphasizes Harold Poppe, “is to work with T-L dealers in designing sprinkler systems that make their farmer customers happy–and that also increase their yields and net income.” He’s the manager of the T-L Pump, Power & Engineering Division that was established last fall. One of its purposes is to stock and have readily available for shipment John Deere and Cummins engines, Cornell and Berkeley centrifugal pumps, self-cleaning suction screens, suction filters, and a complete line of fittings. But, perhaps even more important to farmers, is how the division complements the complete line of T-L irrigation equipment. For instance, an entire combo “package” of sprinkler, engine, and pump that are known to work both reliably and well together under varying conditions can be provided for new installations. An added benefit is that the farmer saves shipping costs if, for example, an engine accompanies his new sprinkler system being sent out from the factory, that saves him the typical hefty $500 to $800 freight charge for shipping an irrigation engine by itself. Amajority of the division’s work involves assisting T-L dealers in designing the most effective and efficient pivot system installation that’s possible for a certain situation. “We like to start working at ground zero.” Poppe says. “We’ll check where the water is and calculate how much is available. Once we have the water supply pegged, we proceed to designing the delivery system in order to exactly provide the required pressure and gallonage for the sprinkler. This includes determining the proper horsepower required to do the job.” Some of the division’s projects also involve diagnosing why a pre-existing pump, engine, and pipe setup isn’t doing the job it’s supposed to. As Poppe observes, “When we trace it back we usually find that a redesign is needed.” This may involve replacing the engine, pump, pipes, or perhaps a combination of changes. The result, he says, is an installation that takes advantage of the best that a T-L system can provide.
![]() | Republic, Kansas |
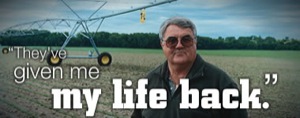
![]() | Laverne, Oklahoma |
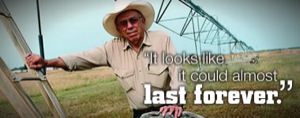
![]() | Rector, Arkansas |
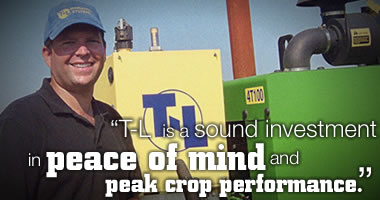
![]() | Strawn, Illinois |
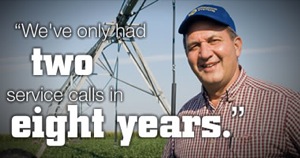
![]() | Allendale, Illinois |
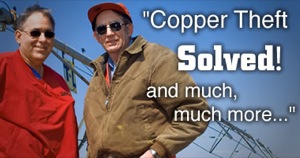
![]() | Newport Arkansas |
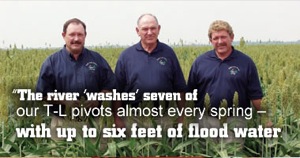
![]() | Great Bend, Kansas |
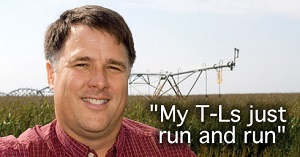
![]() | Beaver, Oklahoma |
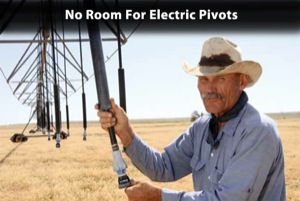
![]() | Rock Port, Missouri |
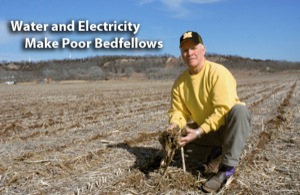
![]() | Plains, Kansas |
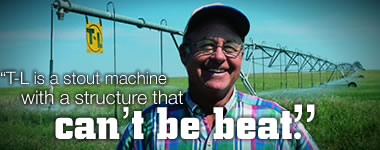
![]() | Laverne, Oklahoma |
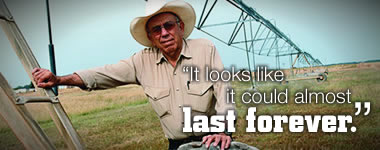
![]() | Beaver, Oklahoma |
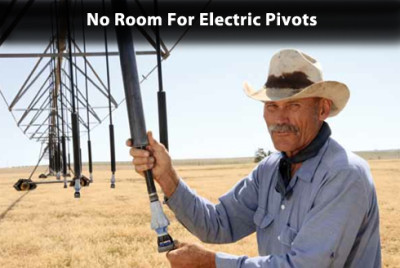
Kurzweil Irrigation
30214 S State Route TT
Harrisonville MO 64701
816-773-6416
Dennis Kurzweil - wcirr@aol.com
17445 Thorn Rd
Jasper, MO 64755
417-825-3095
Russell Dintaman - russell.dintaman@gmail.com
Harrisonville MO 64701
816-773-6416
Dennis Kurzweil - wcirr@aol.com
17445 Thorn Rd
Jasper, MO 64755
417-825-3095
Russell Dintaman - russell.dintaman@gmail.com